Best Practices for Cutting Risk of Stress Corrosion Cracking and Galvanic Corrosion in Water Cooling Systems
Posted November 14, 2017 by Helen Kane
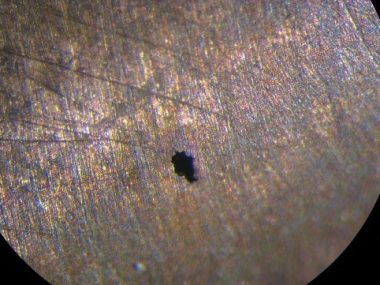
Pitting corrosion causes leaks that lead to equipment failure.
In my role, I have insight into the amazing, world-changing systems our customers develop. These complex, sophisticated designs overcome truly difficult process challenges, but they also can succumb to failure when best practices around water management, stress corrosion cracking or galvanic corrosion aren’t adequately considered.
What’s interesting is that system downtime or process inefficiencies sometimes result from a simple mismatch of materials, for example specifying an aluminum base metal with a stainless steel fastener. We’ve seen instances where the environment and the alloy just don’t dovetail, like when copper is exposed to ammonia.
Take a look at the images I’ve included. I hope that they don’t look familiar! If they do, you already know about the costs associated with solving these problems, and you’ve probably carefully examined your designs to account for stress, conductivity and other factors that we as engineers work so hard to anticipate.
Putting Best Practices into Practice
I’ve put together two best practices guides to help you avoid making mistakes that can restrict water flow, undermine thermal transfer or put device-killing materials into the plumbing that supports your process.
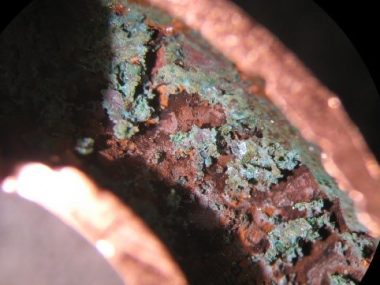
Galvanic corrosion inside this pipe restricts water flow and ultimately cause costly downtime.
On a high level, best practices encompass knowing where the stress load is placed on the system, how the alloys you use are affected by the environment they “live” in, and that the mean time between failure is affected by conditions I’ve just described.
With these best practices guides on hand, you’ll have easy-to-reference reminders you can use to ensure that the cooling systems you build into your tools are effective, and the products you bring to your customers are the best they can be.