Industrial Electric Furnaces: Cost Reduction with SCR Power Controllers
Posted December 04, 2024 by Michael Becker
Blog Summary:
This blog highlights the importance of integrated SCR power controllers in enhancing furnace operations by improving efficiency, reducing costs, and ensuring high product quality. Key points include:
1. Thermal Processing Control Systems: Essential components include Rockwell Automation® Programmable Automation Controllers (PACs), temperature measurement loops (thermocouples or pyrometers), and SCR power controllers for regulating energy input.
2. Integrated Control Architecture: Using components designed to natively connect to the PAC, such as Rockwell Automation’s Logix PAC and Advanced Energy’s Thyro SCR power controllers, can create a synchronized and integrated control system, overcoming challenges with disparate components.
3. Benefits of Integrated SCR Power Controllers: These controllers offer multiple advantages, including greater heater lifetime, optimized power consumption, improved product uniformity, high efficiency (99.5%), minimized parasitic harmonics, balanced heater usage, and reduced utility costs.
This blog highlights the importance of integrated SCR power controllers in enhancing furnace operations by improving efficiency, reducing costs, and ensuring high product quality. Key points include:
1. Thermal Processing Control Systems: Essential components include Rockwell Automation® Programmable Automation Controllers (PACs), temperature measurement loops (thermocouples or pyrometers), and SCR power controllers for regulating energy input.
2. Integrated Control Architecture: Using components designed to natively connect to the PAC, such as Rockwell Automation’s Logix PAC and Advanced Energy’s Thyro SCR power controllers, can create a synchronized and integrated control system, overcoming challenges with disparate components.
3. Benefits of Integrated SCR Power Controllers: These controllers offer multiple advantages, including greater heater lifetime, optimized power consumption, improved product uniformity, high efficiency (99.5%), minimized parasitic harmonics, balanced heater usage, and reduced utility costs.
Silicon-controlled rectifier (SCR)-based power control modules (PCMs) for industrial furnaces need integrated features for precise temperature control, process reliability, product quality and cost-effectiveness.
Thermal processing control systems, such as the Rockwell Automation® Programmable Automation Controller, are fundamental to these operations. In addition, temperature measurement loops are required for control and shut-off. These are typically either thermocouples or pyrometers for harsh environments. Power control architectures that regulate energy input to furnace heaters via SCR power controllers are also essential.
The process temperature is measured during furnace operation and compared to a desired setpoint. The temperature is sent as an input to a PID loop that resides in either the programmable automation controller (PAC) or a temperature controller, depending on the control scheme. This corrective trim signal (4 to 20 mA, 0 to 10 V, Ethernet command, etc.) is then sent to the SCR power controller, which modifies the energy input to the heating elements to reach the desired setpoint.
When it comes to electrical wiring best practices, analog control signal cabling, such as thermocouples, should be kept as short as possible in length and as far away from furnace power cabling as possible to minimize electrical interference. The installation sensitivity to interference typically diminishes when digital communication protocols are used instead of analog signals.
Integrated control architecture
Although some furnace operations’ control systems adhere to and implement installation best practices, they frequently consist of various combined components, rather than forming a highly synchronized network of architectural elements that seamlessly integrate into the control system’s communication and configuration capabilities.
This is a challenge that many furnace installations face.
If the control components are designed to connect directly to the PAC, they become integrated into the PAC architecture with its associated benefits. For instance, the difficulties of combining different components can be addressed through the architectural approach used by the Logix PAC from Rockwell Automation, along with Advanced Energy’s Thyro family of SCR power controllers. With native add-on profiles (AOPs) included in the Rockwell Automation Studio 5000 Logix Designer environment, Thyro SCR power controllers function as integrated parts of an overall control system.
Thermal processing control systems, such as the Rockwell Automation® Programmable Automation Controller, are fundamental to these operations. In addition, temperature measurement loops are required for control and shut-off. These are typically either thermocouples or pyrometers for harsh environments. Power control architectures that regulate energy input to furnace heaters via SCR power controllers are also essential.
The process temperature is measured during furnace operation and compared to a desired setpoint. The temperature is sent as an input to a PID loop that resides in either the programmable automation controller (PAC) or a temperature controller, depending on the control scheme. This corrective trim signal (4 to 20 mA, 0 to 10 V, Ethernet command, etc.) is then sent to the SCR power controller, which modifies the energy input to the heating elements to reach the desired setpoint.
When it comes to electrical wiring best practices, analog control signal cabling, such as thermocouples, should be kept as short as possible in length and as far away from furnace power cabling as possible to minimize electrical interference. The installation sensitivity to interference typically diminishes when digital communication protocols are used instead of analog signals.
Integrated control architecture
Although some furnace operations’ control systems adhere to and implement installation best practices, they frequently consist of various combined components, rather than forming a highly synchronized network of architectural elements that seamlessly integrate into the control system’s communication and configuration capabilities.
This is a challenge that many furnace installations face.
If the control components are designed to connect directly to the PAC, they become integrated into the PAC architecture with its associated benefits. For instance, the difficulties of combining different components can be addressed through the architectural approach used by the Logix PAC from Rockwell Automation, along with Advanced Energy’s Thyro family of SCR power controllers. With native add-on profiles (AOPs) included in the Rockwell Automation Studio 5000 Logix Designer environment, Thyro SCR power controllers function as integrated parts of an overall control system.
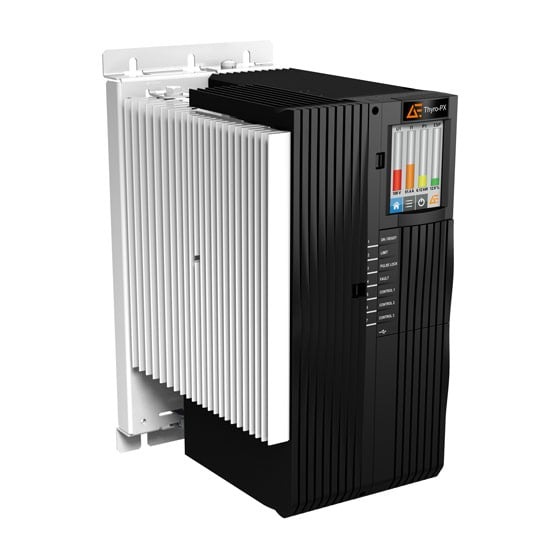
Benefits of the architectural power control module
Integrated SCR power controllers enhance furnace operations by extending heater lifespan, optimizing power use and improving product uniformity.
With an efficiency rate of 99.5%, Advanced Energy's Thyro SCR power controllers offer clear advantages over alternative technologies. Their multiple operational modes, including zero-crossing and phase-angle firing, effectively minimize parasitic harmonics that can decrease transformer lifespans. Additionally, Thyro SCR power controllers balance heater usage and reduce the frequency of on-off thermal cycles. SCR technology can also improve the power factor efficiency available to the furnace and thus reduce utility costs.
The quality of the end product is the ultimate measure of success, alongside operating a furnace economically. Power consumption remains a critical concern for furnace operators, especially when dealing with power sources that have power factors below one. Such inefficiencies lead to increased utility costs and overall expenses. To learn more about how the high efficiency and advanced features of Advanced Energy’s Thyro family of SCR power controllers can help reduce cost for industrial electronic furnace operations visit: Thyro Family | Advanced Energy.
Michael Becker
Advanced Energy
Michael Becker is a product manager within System Power at Advanced Energy.
More posts by Michael Becker