Dynamic Reverse Pulsing in an Industrial Setup: Case Study on SiO2 Deposition
投稿 4月 18, 2023 によって Gayatri Rane
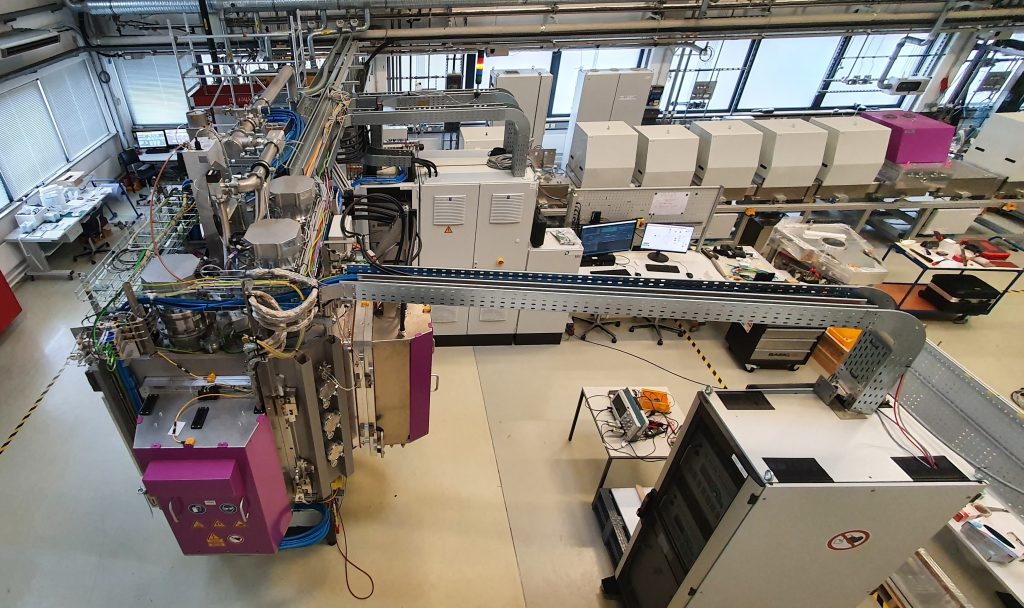
The proof of the pudding is in the eating—that’s our approach at AE’s Customer Solutions Lab in Karlstein, Germany. Testing power delivery innovations first-hand on production-style setups helps us better address our customers’ needs. With new power delivery technologies and techniques, Advanced Energy keeps pace with today’s magnetron sputtering requirements, including the rapid rise in the use of rotatable cylindrical targets and the ever-growing need for thermal-load control onto sensitive substrates.
Any innovation that might replace an existing effective process always faces understandable scepticism. AE introduced Dynamic Reverse Pulsing (DRP) mode a few years ago as an alternative to the conventional bipolar (BP) mode of dual-magnetron processes for reactive sputtering of insulating materials such as SiO2. We used our state-of-the-art Customer Solutions Lab to study DRP’s performance compared to conventional BP mode.
Initial tests on an inline coater at low power density indicated a lower substrate load and a similar deposition rate as BP mode at halved power input P/2 applied at each target (adding up finally to the same total power as the BP mode). This meant lower power loads at each end block.
Continuing our investigations into SiO2 deposition, we added the unipolar (UP) mode of sputtering (Figure 1) to the study. To replicate industrial conditions, we tested the depositions at a higher power load in our industrial drum coater with rotary targets (Figure 2). The coater is highly customizable such that different power modes can be tested with minimal alterations inside the chamber, so that, in essence, reliable comparability between processes can be achieved.
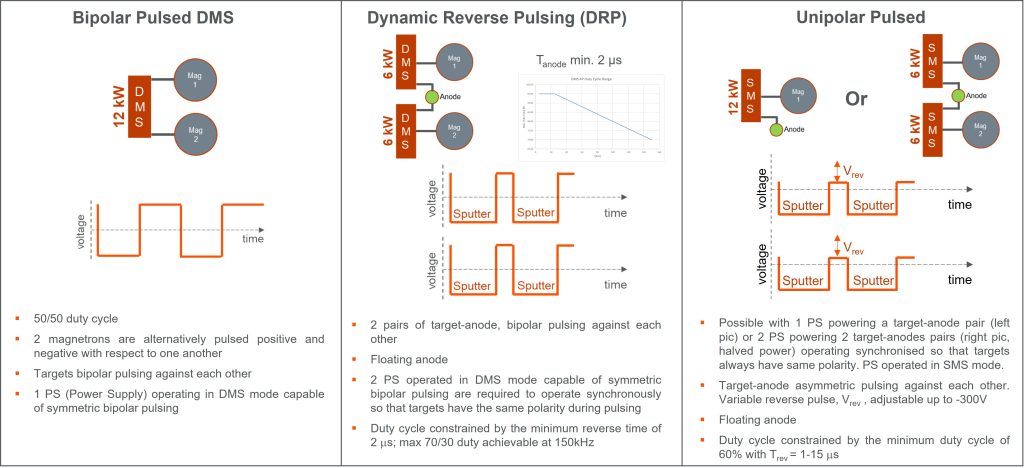
Figure 1. Different power-delivery modes (BP, DRP, and UP) used in this test showing equivalent configurations in terms of total delivered power. Tests were performed at 20 kW/m power density and at 40 kHz and 80 kHz pulsing frequency. 80% duty cycle was used for the DRP and UP modes, and the UP mode was tested with two different reverse voltages (Vrev = 0 V and 200 V).
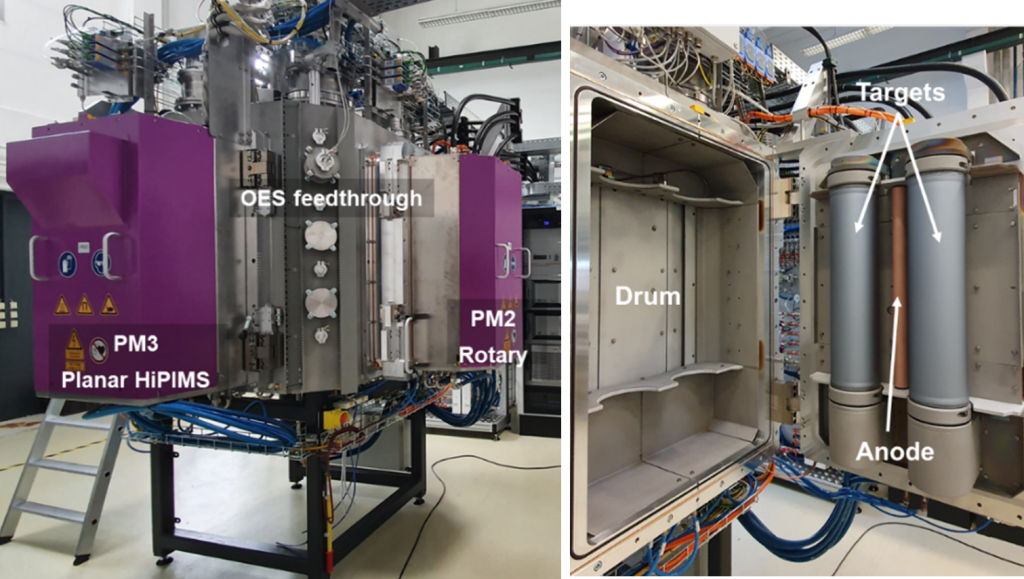
Figure 2. Industrial drum coater (left) and the process door (right) with the dual rotary targets and anode used for the tests
SiO2 films were deposited with the three power modes at 12 kW and 40 kHz, and 80 kHz pulsing frequencies (details in Figure 1). I presented these studies at the SVC Techcon 2022 and the presentation recording is available here for the details. The takeaways are briefly summarised below and in Figure 3.
- DRP and dual-UP modes exhibit many similarities in terms of process parameters as well as film properties.
- ~10% increase in the power normalised deposition rate and ~12% reduction in temperature load on the glass substrate was observed with DRP and dual-UP modes as compared to the BP mode.
- Increase in the pulsing frequency from 40 kHz to 80 kHz led to strong reduction in the arc rate (as can be expected). Operating DRP at a higher frequency lowered the film surface roughness, which may be a consequence of lowered arc rate.
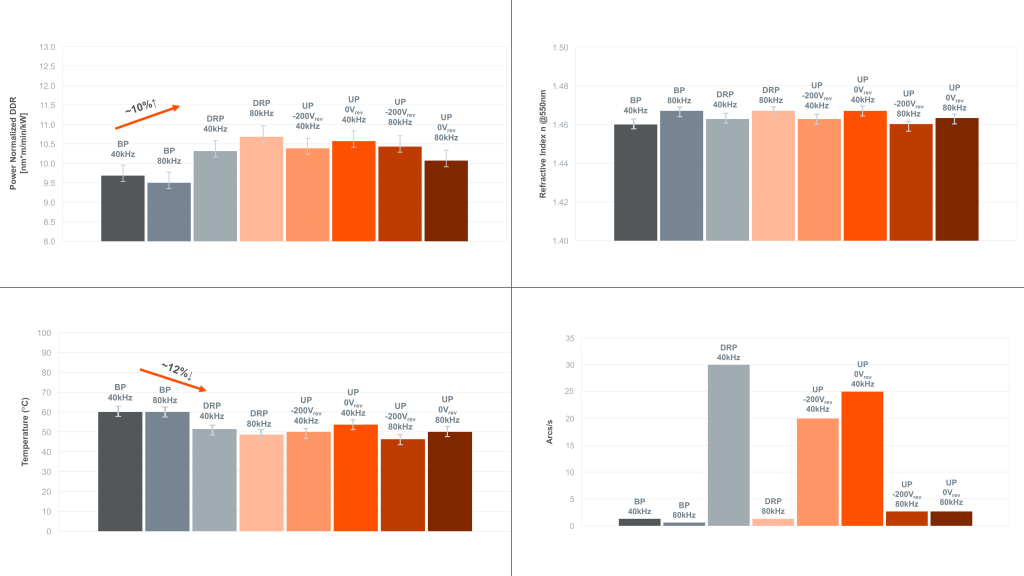
Figure 3. Summary of the results showing the power-normalised dynamic deposition rate, temperature rise at substrate, refractive index, and arc rate for the different modes tested
Besides this, some non-salient features showing differences between the BP mode and DRP/UP (DRP and dual UP clubbed together due to several similarities) mode were noted:
- The DRP/UP modes operate at lower discharge voltages as compared to the BP mode and required lower O/Ar gas flow ratio to operate at similar working point in the transition region.
- The discharge current is almost halved on each side of the magnetron-anode pair in the DRP/UP modes compared to the BP DMS current. The total discharge current (sum of both sides) is around 10% higher in the DRP/UP mode.
- Optical emission spectroscopy (OES) showed that the ratios of different gas species (normalised to Ar line) were similar between the DRP/UP modes but differed from the BP mode. A higher O/Si ratio in the plasma was observed for the BP mode. When DRP and BP modes yielded similar deposition rates (i.e., deposited at different working points in BP and DRP mode), the O/Ar and Si/Ar ratios still differed. This indicates inherent differences in the plasma characteristics between the different modes.
- A higher intensity of the plasma closer to the substrate was recorded with OES for the BP mode as compared to the DRP/UP modes. The farther spread of the plasma, in the BP mode, towards the substrate is affected by the substrate movement and leads to fluctuations in the line signal. These perturbations were also then reflected in the output power in the BP mode and can have an impact on the process stability depending on the extent of the fluctuations.
Follow this blog for future posts delving deeper into DRP mode, and watch more of AE’s narrated SVC TechCon presentations on the SVC YouTube channel:
- AE’s RF and DC Power Solutions for Next Generation PECVD and PVD Industrial Applications
- Power Factor Improvement for Roll-to-Roll Vacuum Coating Systems Using SCR Power Controller in Voltage Sequence Control
- Advanced Energy’s Customer Solutions Lab
- Reactive Sputter Deposition: Effect of Different Power Configurations – A Case Study
Advanced Energy’s global Customer Experience Centers and Collaborative Development Centers provide an important collaboration space for engineering teams to work together and solve customer design challenges. Learn more about AE’s capabilities here. We look forward to partnering with you to solve your design challenges.