Taking the Temperature of Innovation
게시됨 11월 04, 2024 으로 Tim Dubbs
State-of-the-art high precision thermal measurement
solutions for today’s demanding manufacturing processes
solutions for today’s demanding manufacturing processes
Key Takeaways:
1. Importance of Temperature Monitoring: Essential for ensuring high product quality, maximum throughput, and optimized yield in industrial manufacturing.
2. Shift to Advanced Technologies: Traditional thermocouples and thermistors are being replaced by more sophisticated optical techniques for better reliability and repeatability.
3. Fiber Optic Sensors:
5. Optical Pyrometers:
1. Importance of Temperature Monitoring: Essential for ensuring high product quality, maximum throughput, and optimized yield in industrial manufacturing.
2. Shift to Advanced Technologies: Traditional thermocouples and thermistors are being replaced by more sophisticated optical techniques for better reliability and repeatability.
3. Fiber Optic Sensors:
a. Versatility: Can measure temperature, strain, pressure, and deflection.
b. Advantages: Thin, flexible, immune to EMI, and often do not require recalibration.
b. Advantages: Thin, flexible, immune to EMI, and often do not require recalibration.
c. Techniques:
i. Phosphor Decay Sensors: Measure temperature based on the decay time of light emitted by phosphor.
ii. Fiber Bragg Grating (FBG): Uses light spectrum changes to measure temperature and other parameters.
iii. Fabry Perot (FP) Interferometric Sensing: Measures temperature and pressure using reflected waveforms.
4. Applications of Fiber Optic Sensors: Widely used in semiconductor manufacturing for precise temperature measurement in environments with strong RF EMI fields. Examples include Advanced Energy’s Luxtron® M-1100 and WaveCapture™ FBG Analyzer.5. Optical Pyrometers:
a. Non-Contact Measurement: Measures thermal radiation without touching the surface.
b. Advantages: Simplifies setup, avoids influencing the material’s temperature, and can measure a wide range of temperatures.
c. Applications: Suitable for various materials, including metals, plastics, and glass. Used in semiconductor and thin film technology production.
d. Examples include Advanced Energy’s 4100T and UVR 400 pyrometers.
6. Summary: Modern temperature measurement technologies like fiber optic sensors and optical pyrometers provide significant advantages over traditional methods, including immunity to EMI and non-contact measurement, making them ideal for contemporary industrial applications.
b. Advantages: Simplifies setup, avoids influencing the material’s temperature, and can measure a wide range of temperatures.
c. Applications: Suitable for various materials, including metals, plastics, and glass. Used in semiconductor and thin film technology production.
d. Examples include Advanced Energy’s 4100T and UVR 400 pyrometers.
Many industrial manufacturing processes require monitoring and control of temperature at key points in the operation to ensure the highest product quality, maximum throughput and optimized yield. To meet these demands, innovations are driving new precise and reliable thermal measurement solutions. Traditional technologies such as thermocouples and thermistors are giving way to more sophisticated optical techniques that deliver improved reliability and repeatability needed by modern thermal processes. This has led to the growing use of fiber optic sensors that are immune to electromagnetic interference (EMI) common in industrial environments, and non-contact pyrometers that measure precise thermal radiation.
Fiber Optic Sensors
Fiber optic technology is incredibly versatile as it can transmit high speed data in networking systems and can measure physical parameters including temperature, strain, pressure and deflection. What’s more, the technology is flexible; individual fibers are thin, have few length constraints and multiple sensors and sensor types per fiber. Fiber optic has also been shown to be a mature and robust technology when proper care is taken in installations and does not suffer from mechanical fatigue (ideal for industrial applications). In addition, in many applications, there is no need for recurring calibration. Another important benefit is that fiber optics are completely insensitive to any form of EMI, which is a particularly important benefit in an electrically noisy environment.
There are many techniques in which fiber optics can be used for temperature measurement. Phosphor decay temperature sensors (aka FluorOptic® thermometry platform), for example, pulse light into phosphor in contact with the surface and then measure the light emitted by the phosphor
Fiber optic technology is incredibly versatile as it can transmit high speed data in networking systems and can measure physical parameters including temperature, strain, pressure and deflection. What’s more, the technology is flexible; individual fibers are thin, have few length constraints and multiple sensors and sensor types per fiber. Fiber optic has also been shown to be a mature and robust technology when proper care is taken in installations and does not suffer from mechanical fatigue (ideal for industrial applications). In addition, in many applications, there is no need for recurring calibration. Another important benefit is that fiber optics are completely insensitive to any form of EMI, which is a particularly important benefit in an electrically noisy environment.
There are many techniques in which fiber optics can be used for temperature measurement. Phosphor decay temperature sensors (aka FluorOptic® thermometry platform), for example, pulse light into phosphor in contact with the surface and then measure the light emitted by the phosphor
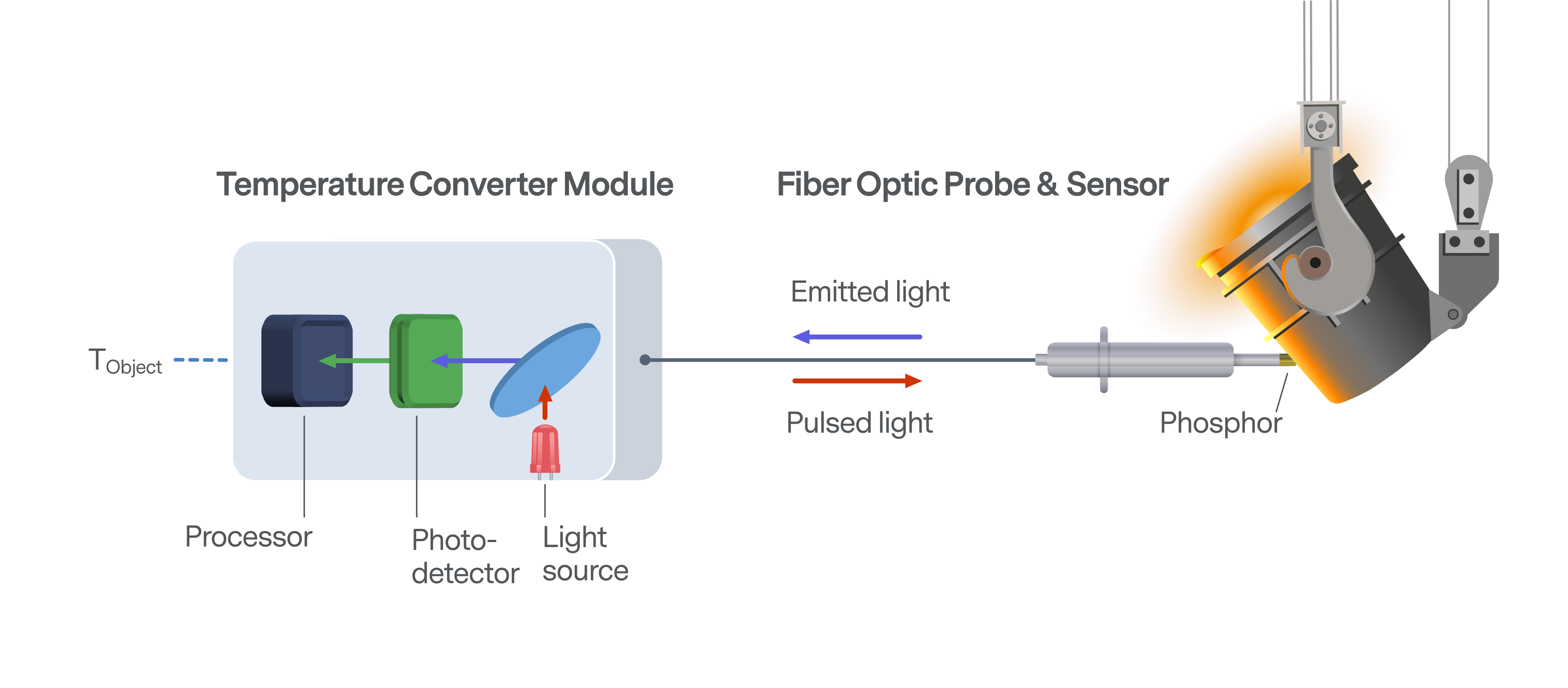
The underlying principle is the decay time of emitted light (Tau Decay) is tightly related to the phosphor's temperature. By accurately measuring the decay time, temperature can be calculated. Since this technique is not intensity based, but rather time decay, it is highly resistant to fiber attenuation losses and contaminated or loose connections.
An alternative method, known as Fiber Bragg Grating (FBG), uses fiber optics with FBG sensors patterned into the fiber at desired positions. A wideband light source is used to project a light spectrum down the fiber, each sensor reflects back a single unique wavelength to a spectrum analyzer or interrogator. Any temperature changes will cause small wavelength changes that can be analyzed by a spectrometer (often called an “analyzer”).
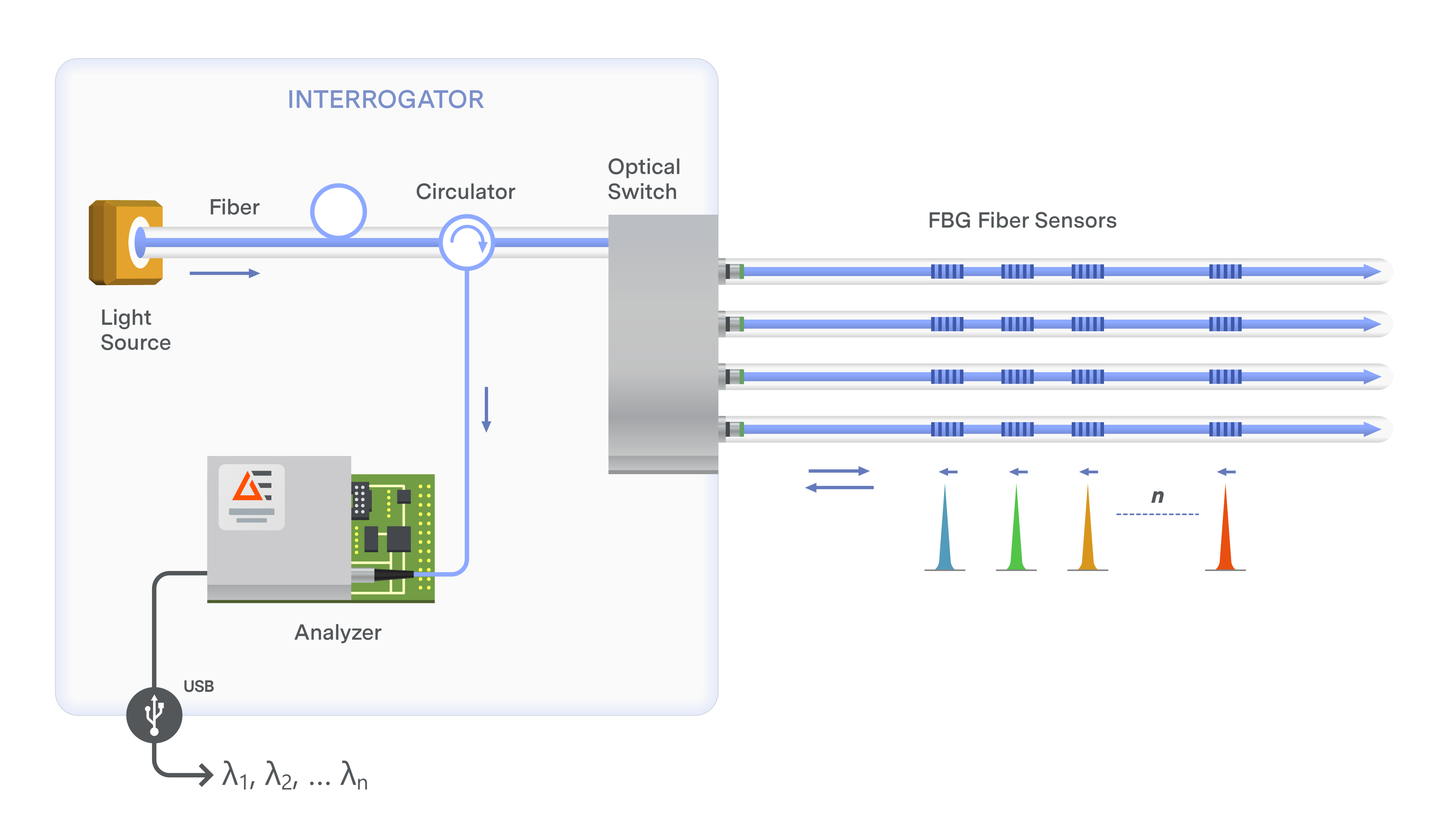
As well as temperature, the FBG approach allows for multipoint measurement of parameters (such as strain and vibration) and, as it only requires a single fiber, is minimally invasive.
A third method, known as Fabry Perot (FP) interferometric sensing, is capable of sensing pressure as well as temperature using a pressure sensitive capillary cell that is built within the fiber. The temperature measurement (known as “Intrinsic FP”) is based upon the reflected waveform.
A third method, known as Fabry Perot (FP) interferometric sensing, is capable of sensing pressure as well as temperature using a pressure sensitive capillary cell that is built within the fiber. The temperature measurement (known as “Intrinsic FP”) is based upon the reflected waveform.
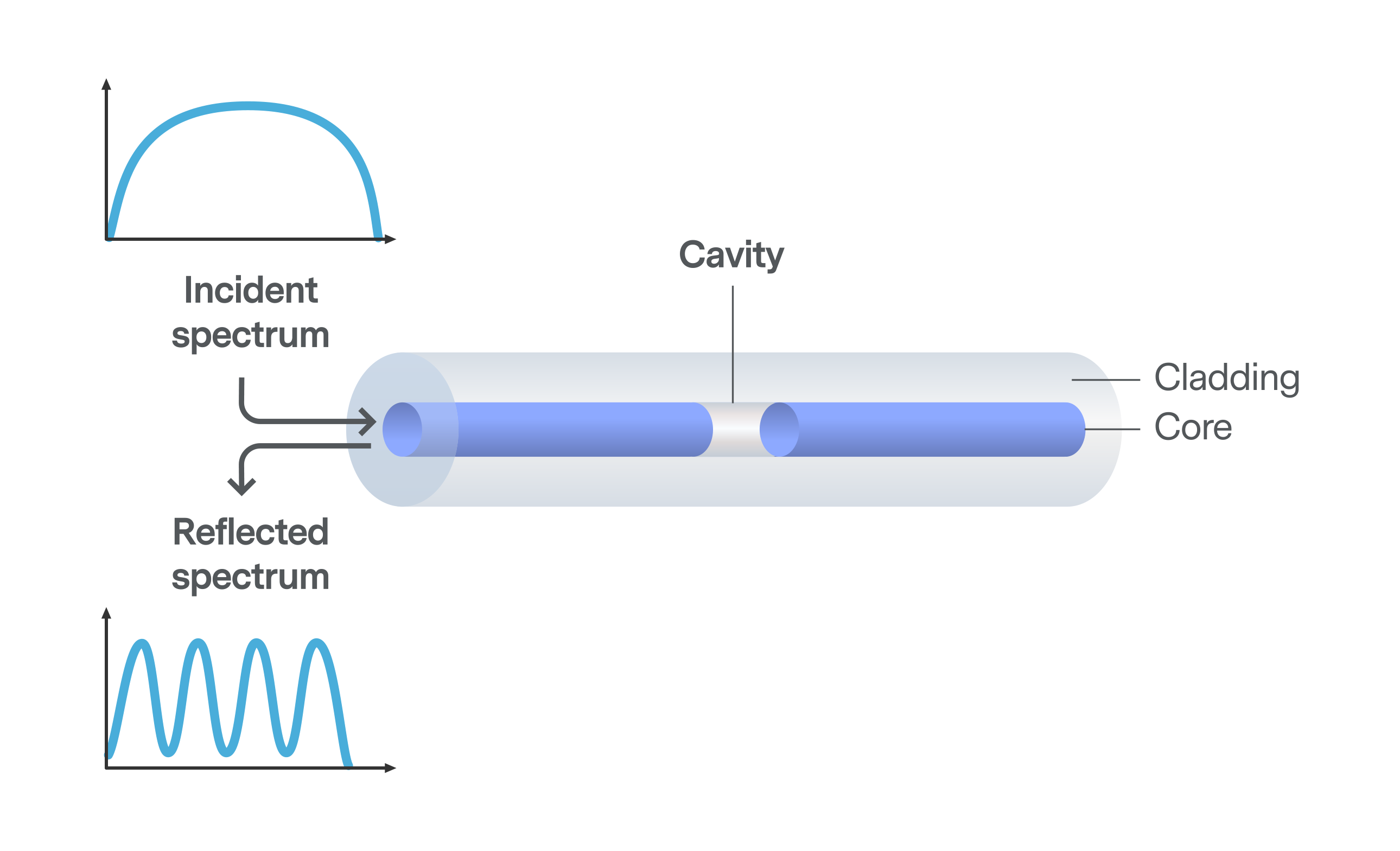
The same analyzer that is used for FBG analysis can also be used for FP, allowing for flexibility and commonality when designing manufacturing processes.
Fiber Optic applications and solutions
Along with the many industrial applications for fiber optic temperature measurement, this technology brings specific benefits within the semiconductor manufacturing industry – especially for etch and deposition processes. Here, fiber optics facilitate the high precision temperature measurement of electrostatic chucks, wafers, chamber lids and walls within the presence of very strong RF EMI fields, and plasma.
A good example of this type of technology can be found in Advanced Energy's Luxtron® M-1100 FluorOptic® five-channel thermometry (FOT) converter. This includes an advanced light source, offers low noise and rapid response and, thanks to new proprietary phosphor formulations VioLuxTM and RubiLuxTM, delivers 0.5°C accuracy (without further calibration), repeatability, and stability over an extended temperature range covering -200 to 450°C. Multiple communication outputs are available, including an optional EtherCAT interface.
Along with the many industrial applications for fiber optic temperature measurement, this technology brings specific benefits within the semiconductor manufacturing industry – especially for etch and deposition processes. Here, fiber optics facilitate the high precision temperature measurement of electrostatic chucks, wafers, chamber lids and walls within the presence of very strong RF EMI fields, and plasma.
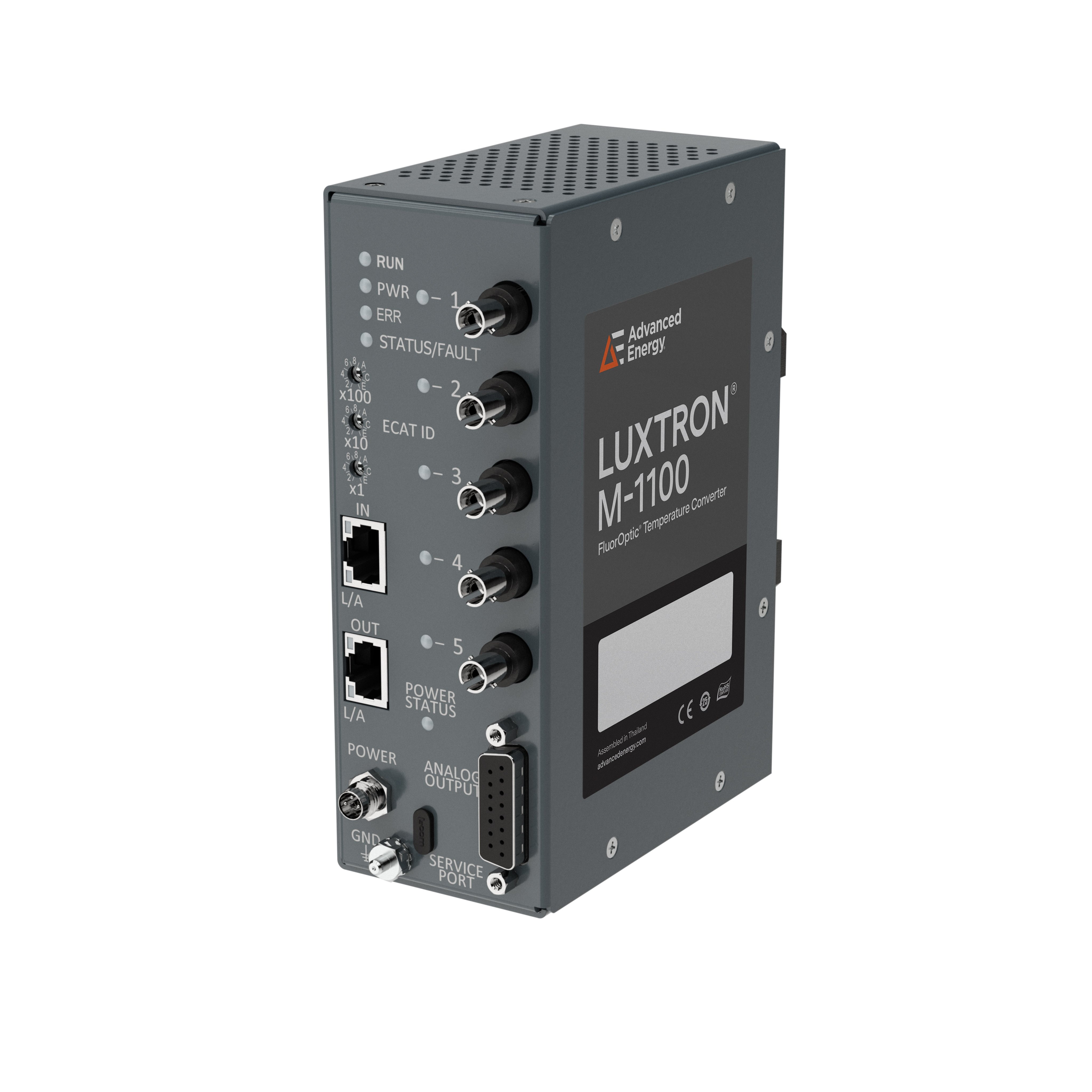.jpg)
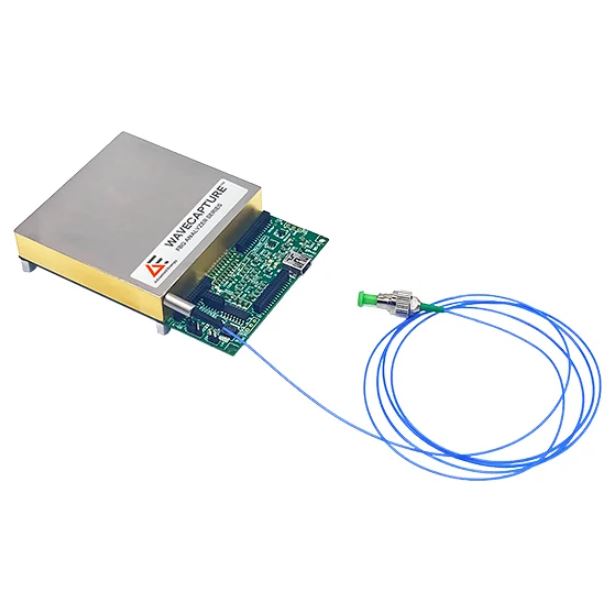
Another example is Advanced Energy’s WaveCapture™ FBG Analyzer, which produces an innovative, high-efficiency, optical design that is hermetically sealed. The system delivers excellent wavelength repeatability and resolution as well as long-term stability, ultra-low power consumption and rapid response. The system can be used in harsh environments with no maintenance or calibration required and is field-proven, with thousands of units deployed globally.
Optical Pyrometers
While traditional temperature measurement methods require contact with the surface being measured, optical pyrometers use a non-contact method to optically measure the emitted thermal radiation and then convert this into a temperature reading. A key advantage is the lack of contact which simplifies set-up and installation while ensuring the device does not influence the temperature of the material being measured.
While traditional temperature measurement methods require contact with the surface being measured, optical pyrometers use a non-contact method to optically measure the emitted thermal radiation and then convert this into a temperature reading. A key advantage is the lack of contact which simplifies set-up and installation while ensuring the device does not influence the temperature of the material being measured.
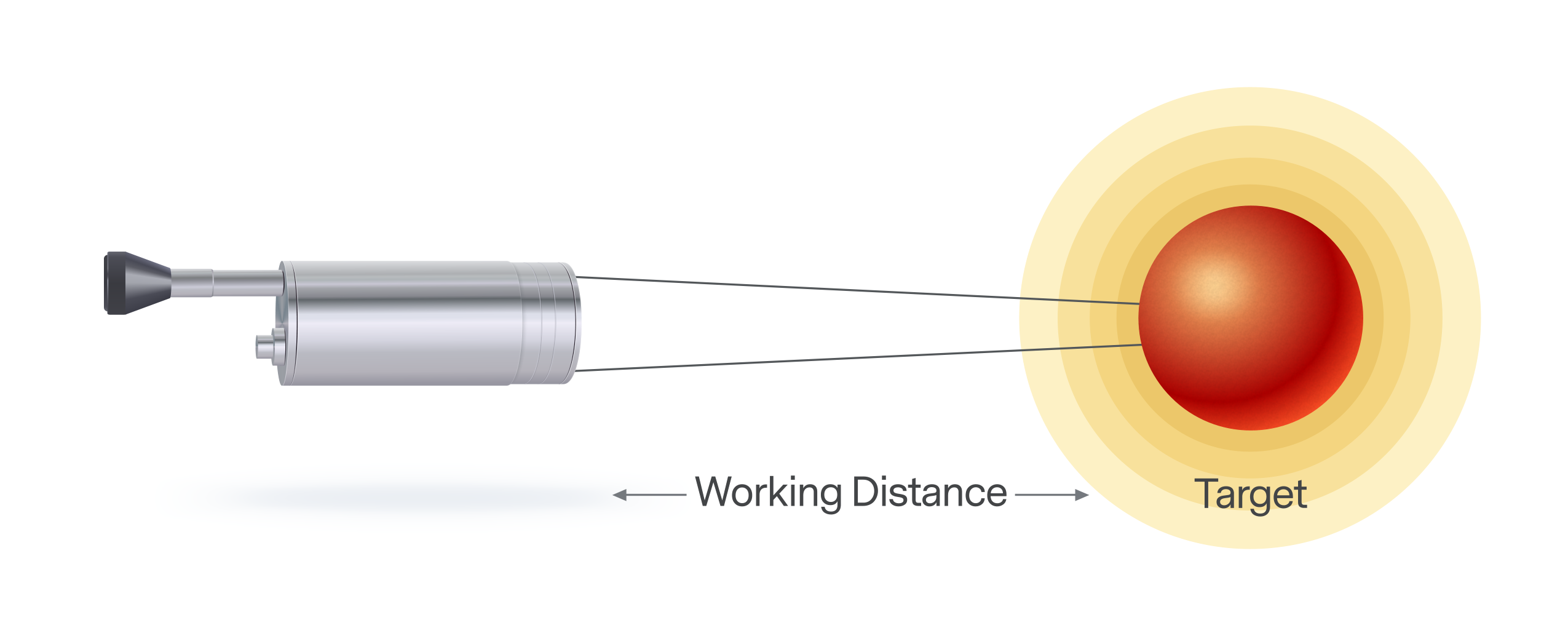
It is common to use a wavelength-specific filter based upon the materials being measured to block unwanted energy and measure only a specific wavelength. Selecting the correct wavelength determines the range of measurement as well as minimizing challenges associated with material dependent emissivity effects.
With some detector choices it is possible to measure low (sub-0°C) temperatures using this approach; however, the emitted radiation is low, and care must be exercised. It is important to use a pyrometer tailored to the specific process as different surfaces such as metallic, non-metallic, glass and special materials require different solutions.
Optical Pyrometer Applications and solutions
Pyrometers can be used for a wide variety of applications including metallic surfaces and non-metallic surfaces ranging from plastics, paper and wood to foodstuffs, clay and asphalt. They also play an increasingly important role in the production of glass and in specific processes for fabricating semiconductors and thin film technology.
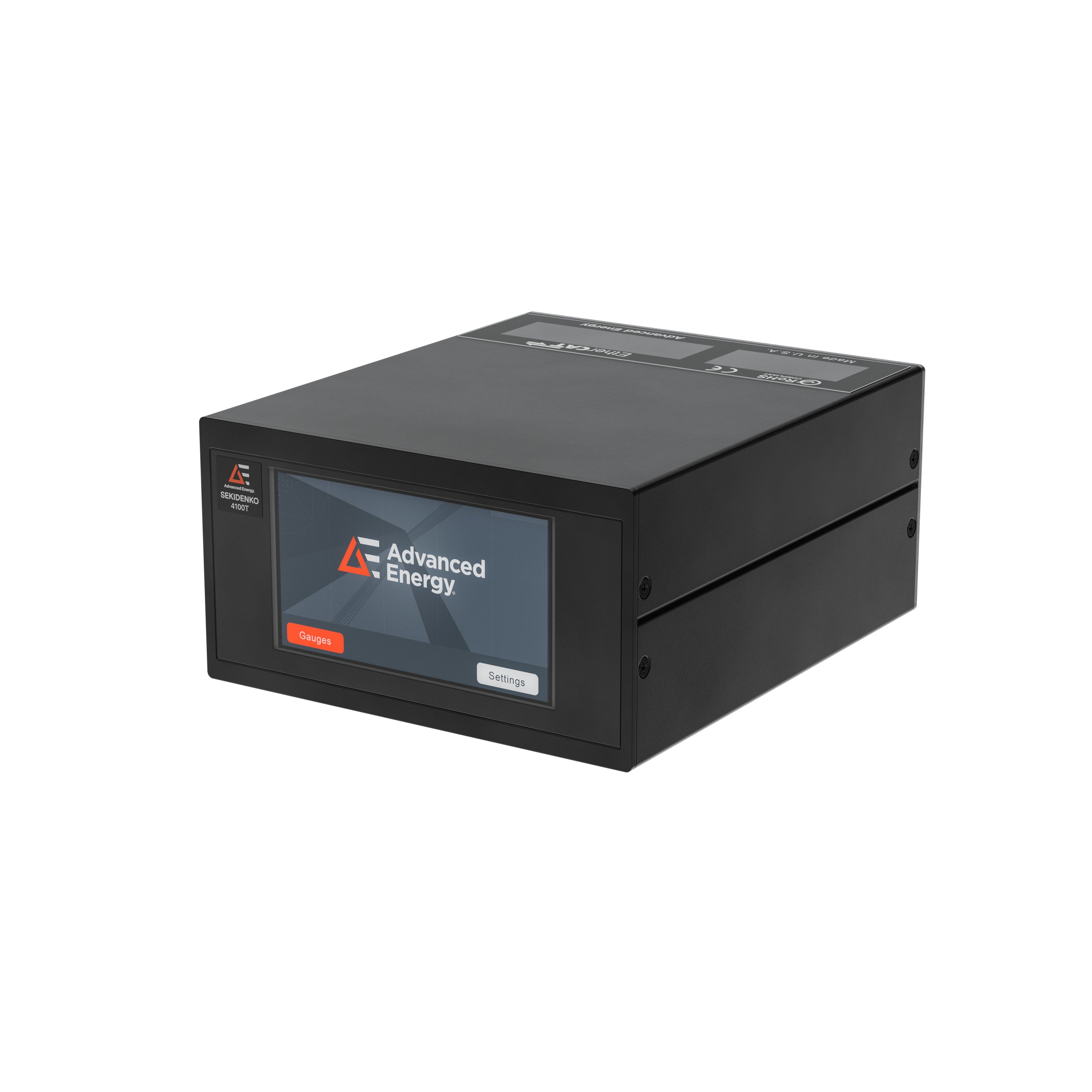
Advanced Energy is a leader in the development of optical pyrometers with products such as the Sekidenko 4100T, a new version of its special materials pyrometer that provides the high-accuracy, non-contact temperature measurement. The upgraded 4100T provides simultaneous, high-speed (1kHz) measurements on up to four channels. Each channel can be configured independently, with wavelengths ranging from Ultraviolet to 2,300 nm, and temperature ranges spanning 60°C to 3,000°C.

Advanced Energy also offers the UV 400 and UVR 400 digital pyrometers, which are designed specifically for GaN-based MOCVD epitaxy processes where they provide direct measurement of the wafer surface temperature. This delivers significant improvements over the traditional susceptor/pocket temperature measurement, leading to enhanced yield. The UVR 400 pyrometer incorporates an additional reflectometer at 635 nm, facilitating the measurement of deposition thickness and the system hugely improves LED production processes where there is a strong correlation between process temperature and the final product wavelength.
Summary
Temperature measurement is incredibly important to the control and accuracy of many manufacturing processes. In the past, technologies such as thermocouples or thermistors were primarily used for this. However, these are susceptible to EMI and are intrusive in nature making them less than ideal for modern demands.
Fiber optic temperature measurement eliminates the EMI issues entirely and brings additional benefits such as eliminating the need for regular recalibration. Optical pyrometers are suitable for a wide range of temperatures and offer the additional benefit of not requiring contact with the material being measured.
Summary
Temperature measurement is incredibly important to the control and accuracy of many manufacturing processes. In the past, technologies such as thermocouples or thermistors were primarily used for this. However, these are susceptible to EMI and are intrusive in nature making them less than ideal for modern demands.
Fiber optic temperature measurement eliminates the EMI issues entirely and brings additional benefits such as eliminating the need for regular recalibration. Optical pyrometers are suitable for a wide range of temperatures and offer the additional benefit of not requiring contact with the material being measured.

For more information on Advanced Energy’s temperature sensing solutions, visit here: Temperature Sensing | Advanced Energy.
Tim Dubbs
Advanced Energy
Tim Dubbs is Advanced Energy’s Director, Apps Engineering – Industrial Power, System Power.
더 많은 게시물 Tim Dubbs