So, You’re Still Wasting Money on Solid-State Relays?
已发布 十一月 28, 2017 由 Advanced Energy Editor
First, let me say that I respect solid state relays for the work they’ve done. Compared to their predecessors, mechanical contactor technology, they took control and reliability to a new level in industrial automation processes…
...But that level isn’t high enough to meet today’s demand for more accurate automation control and lower cost operations.
Where I’m going with this is that multiple automation control improvements can be achieved by replacing these old technologies with next-generation digital SCR power controllers (or PCMs for short). Whether you are an OEM or end-user, PCMs that provide increased functionality, take up a smaller footprint and by nature can be integrated into the automation control architecture can enhance your process control, improve end-product yield and repeatability, and reduce your utility and maintenance costs at the same time.
Okay, okay, you’ve heard this kind of marketing message before. However, let me give you an example that will begin to prove what I’ve just said.
Let’s consider the example of infrared heating used in electric furnaces, ovens and heaters.
In infrared heating applications, where significant power fluctuations and switching are inherent, using solid state relay (SSR) technologies can create significant process control problems.
Let me explain. An SSR has two states – on or off – and they are controlled by an external source. The problem is that if the SSR switches state when the power output is not zero, a significant amount of noise and harmonic distortion is created. Total harmonic distortion (THD) has the unpleasant effects of skewing power consumption levels, has adverse effects on power factors and ultimately reduces heater and transformer lifetimes.
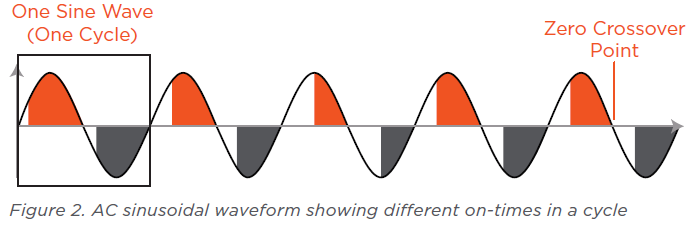
Conversely, the control functionality available with PCM technology enables the on/off switching of heaters and transformers to be at the zero crossover point of the AC power input – irrespective of whether it is single-phase or 3-phase. As a result, thermal inertia, harmonics and heat flicker in the heater elements are minimized, and the overall power factor is higher. Heater and transformer lifetimes are extended, which translates into lower maintenance and total cost of ownership (TCO). (As an aside, this approach conforms to the IEEE 519-2014 Recommended Practice and Requirements for Harmonic Control in Electric Power Systems.)
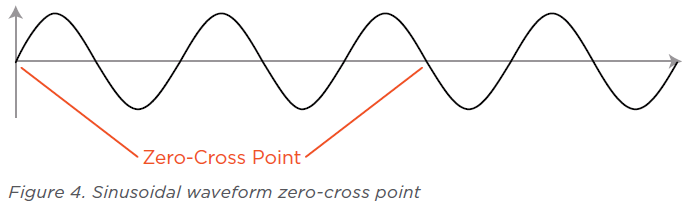
So, with this said, you might be convinced that SCR power controllers are the right way to go. But how do you differentiate between the many vendors available?
In the end, it all comes back to productivity. An ideal SCR controller will have all the functionality that you need to control power factor, minimize THD, and handle both single-phase and 3-phase supplies (irrespective of whether these are "dirty power" sources or not).
Now, all of this is great, but the real key is whether the PCM is just a stand-alone component in the process or whether it is a tightly integrated architectural element tied into the overall control system. We believe that the PCM should be able to natively integrate into the control system’s communication and configuration capabilities, saving users both time and money – whether it be at initial installation or in the full production environment – and we’ve developed our Thyro SCR power controllers to do exactly that.
So, while I don’t expect this one example to convince you that digital SCRs will help you stop wasting money, I do think it would be a good investment of your time to further explore the better process control that SCR controllers can bring to your application.
For more information, check out this infographic, which gives more details on the reliability, control and operating cost advantages to the example I gave above.